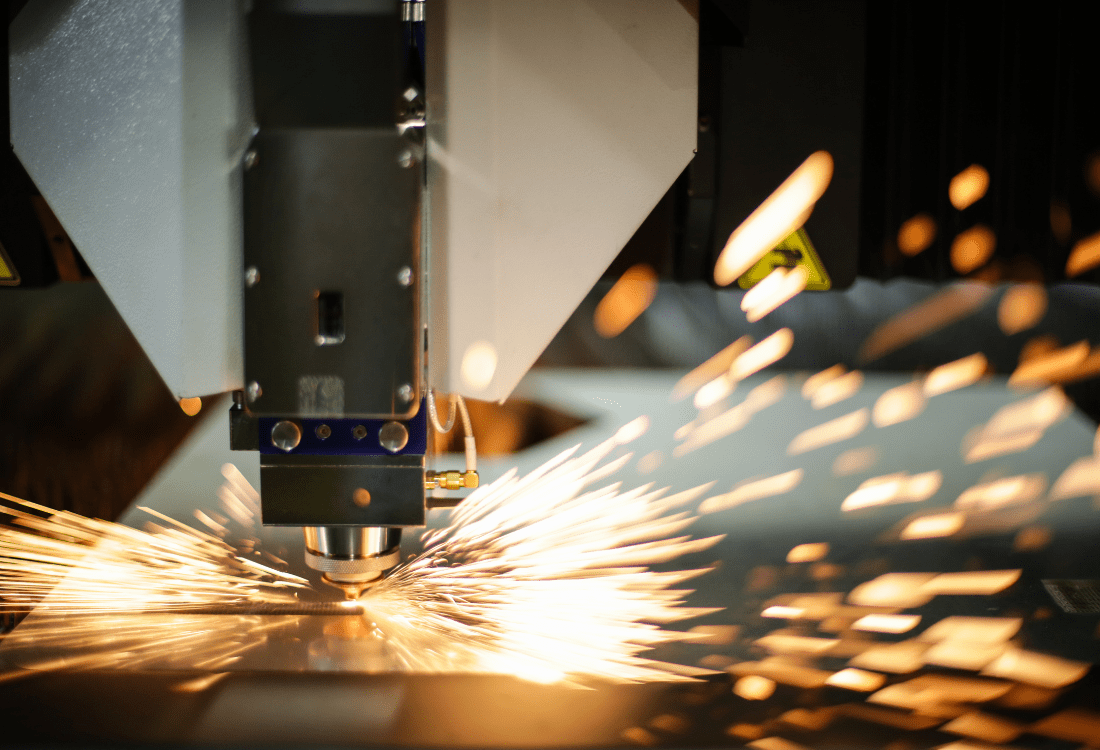
The Benefits Of Using Laminates That Do Not Contain ABS
Acrylonitrile Butadiene Styrene, more commonly known as ABS, is a highly versatile thermoplastic material. It is very hard wearing and durable so is often used for furniture and high traffic spaces. It can withstand most household cleaning products, as well as being both low level-heat and water resistant. It won’t warp or lose shape and is generally considered to be a more sustainable option than PVC.
However, although ABS has numerous advantageous qualities, it is not always the best choice when making products using a laser cutter. Ideally, laser cutting materials need to be able to produce neat and clean edges, withstand extreme levels of heat during cutting and ideally produce few if any harmful chemicals. Unfortunately, on a few of these metrics, ABS falls a little short. Which is why it is generally best to use non-ABS laminates, as you can see below.
Improved Cutting Precision
Laser cutting ABS plastic makes incisions at very high temperatures, and being a thermoplastic, it tends to melt and burn. This creates unclean edges, and the material does tend to fuse around the cuts. What this means in practice is that fine cuts are not possible on laminates containing ABS, and it is also prone to warping. If you are looking to make very precise and neat cuts, then it’s generally best to use a non-ABS variety laminate. This will increase the levels of precision in your cutting and reduce the risk of incisions fusing once cut.
Reduced Toxicity
Laser cutting ABS fumes contain a wide range of toxins. Among these are some benzene derivatives which can be hazardous to health. There are specific dangers about inhaling fumes but also repeated exposure can cause skin irritation. This happens as a result of the laser energy causing the polymer to degrade into multiple components, releasing ultrafine toxin particles and VOCs. Laminates that don’t contain ABS are therefore beneficial for the wider environment but also for the health of anyone operating a machine. However, it is also strongly recommended that any laser cutting machine should be fitted with an efficient and certified fume removal system to ensure operative safety at all times.
Reduced Fire Risk
Laser cutting on plastic containing ABS can be considered a fire risk, as it is susceptible to high levels of heat. When higher levels of heat are applied, there is a lack of removal of material either by char or volatility which can lead to extreme levels of local heating and even ignition. Using non-ABS laminate will lower or even eliminate that risk, keeping all operatives and property safe.
Increased UV Exposure
ABS has a relatively poor level of solvent and fatigue resistance. It also tends not to stand up well to prolonged UV exposure and weathering unless some form of protection is applied. Laminates without ABS will generally have a higher resistance to UV exposure and won’t need as much protection, this reduces both the cost and timescale of projects.
ABS has its place but, as you can see, it is generally not a good idea to use ABS-based materials for laser cutting. However, there are plenty of alternative materials out there that can be used in its place. To find out more about laminate laser cutting and laser cutting on plastic contact us to speak to a member of the team.
Image Source: Canva