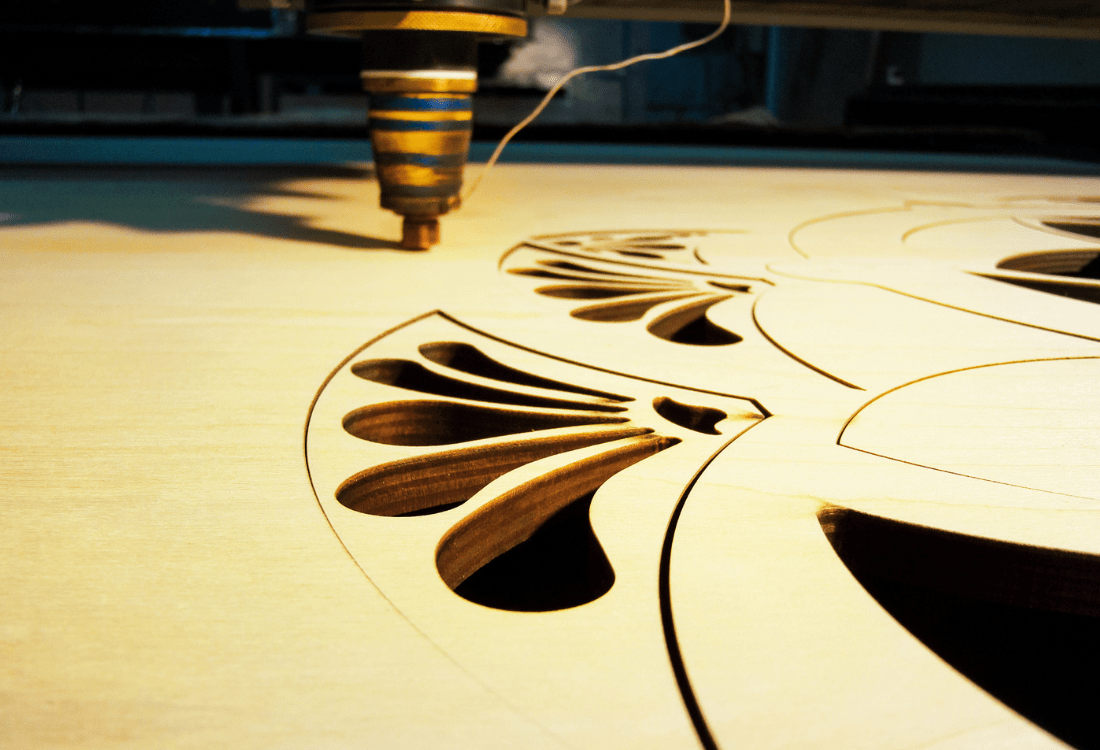
Factors Model Makers Should Consider When Using Wood For The 1st Time
Wood is an incredible material. Not only is it completely sustainable, as it can be endlessly regrown (providing natural benefits to the landscape and air quality levels), but it is also flexible, versatile, durable and comes in a huge range of tones, shades and finishes.
It can be painted, varnished, waxed or treated in various other ways, and if the surface starts to look tired and worn (or if you simply don’t like it) it can be sanded down and done again.
Wood also has a huge range of uses in everything from construction and shipbuilding to sporting equipment and furniture. It’s also incredibly popular with model makers, mostly for the reasons outlined above, but also because it can be easily worked. Wood can be sanded, cut, planed, carved or otherwise manipulated into a huge range of shapes. It can be fastened together with nails, screws, glue or simple carpentry joins. And it’s strong too, making it one of the ideal laser cutting materials.
However, it’s also important to know that wood is a natural material and therefore has properties that can evolve and change. No two bits of wood are exactly the same and may react, age or move differently over time. It can often take years to gain a full understanding of how the different wood types behave. For model makers starting out with wood, it is very useful to try and understand a few of the key principles to bear in mind when working with this incredible material. So, knowing what wood to use for laser cutting means thinking about a few things, including:
Moisture Levels
All wood used by model makers will contain moisture when it is first harvested from the tree. The tree sucks up water through its roots and distributes it around its branches and leaves through a network of pathways in its trunk. Once cut, this moisture will start to dry but this may take some time, even months or years to fully season. Moist wood is more difficult to cut and shape but, similarly, if the wood is too dry it is much more susceptible to burning or charring when laser cutting. As burnt designs tend to look less professional, some woods might benefit from added moisture and others less.
Knots And Rings
Almost all wood grows in annual cycles so it features ring grain, as well as knots and other imperfections. It’s all part of the character of the material but can also make cutting and etching more problematic. If you really don’t want these to feature in your end product you can choose wood with tighter or less visible grain and no knots. This may involve paying for more expensive wood or selecting sections without these traits. But in general, these form an important part of the aesthetic. Beginners will need to be careful when cutting or etching around these areas as the texture and hardness can be different.
Light Or Dark Colours
Wood comes in a wide choice of hues and tones, generally ranging from light-coloured to dark. Light wood tends to be better for laser engravings as the renderings will be more prominent due to a higher contrast. The etchings on dark-coloured wood tend to be harder to see so it all depends on your style of design and project requirements.
Resin
Just as wood contains water, it also contains resin and the resin levels can have a significant impact on the end product. The higher the resin levels in the wood, the darker the etch will be, and therefore the more striking and contrasting the results. If you require a more subtle effect, wood pieces with a lower resin content are recommended. Different woods have different levels of resin and even different sections of the same tree. For example, heartwood contains much higher resin levels than exterior sections. Again, wood used by model makers is always better when properly aged so that moisture and resin levels have dropped to the required levels.
To find out more about the cutting and engraving potential of laser cutting for wood, or to get the right laser cutter for wood projects, contact us to speak to a member of the team.
Image Source: Canva